DESIGNING A CLOSED-LOOP RECYCLING SYSTEM FOR THE UNIVERSITY OF CALIFORNIA, BERKELEY

Problem Statement
​
The world is undergoing a plastic waste crisis. Islands of plastic now reside in our oceans. Invisible microplastics have contaminated our food and water. As part of its National Sword policy, China has cracked down on the types of plastic it will accept, leaving American recycling facilities scrambling to find more ethical and local methods to process plastic waste [1].
​
Against such an ecopolitical backdrop, consumer pressure for companies to go green has mounted. Unfortunately, most companies are simply greenwashing their operations, and their supposedly sustainable products aren’t as “green” as promised. For example, although PLA, a composite polymer derived from bioproducts such as corn and cassava root, is widely marketed as a completely compostable plastic, intensive biodegradation is required and most facilities lack the financial resources to process this material [2]. According to a report from Samantha Lubow, the Environment Initiatives Coordinator for CalDining, UC Berkeley purchases roughly 3 million disposable PLA products every year [3]. Even if students compost these products, the facilities simply cannot afford to process them, and the material goes to waste.
​
Recently, PLA has become popularized in medical research, especially in conjunction with 3D printing, since PLA is non-toxic and is good for detail work [4]. However, as pointed out in their introductory 3D printing training, the Makerspace at UC Berkeley points out the myriad of issues a designer can encounter during 3D printing, ranging from too much extrusion to too little infill. 3DMC, the 3D printing organization on campus, estimates that 50% of prints fail. With over a hundred 3D printers on the UC Berkeley campus, failed prints are mostly sent to the landfill, which is not only a waste of resources but is harmful to the environment [5]. This problem can be alleviated through implementing a closed-loop system that collects failed prints and recycles them into viable 3D printing filament.
​
Our project currently caters to the UC Berkeley campus, but sustainable 3D printing filament will easily catch on in other campuses and other makerspaces. At UC Berkeley, the standard membership cost for makerspaces is $100 per semester, which can be expensive for many students. By giving schools the technology to make full use of PLA waste as a resource instead of a liability, we will not only make 3D printing more sustainable by implementing circular economies, but also more affordable and accessible to future innovators.
​
History

Spring 2016
Nikki Panditi and Scott Silva were awarded a TGIF mini-grant to fund granulator and extruder

Spring 2018
Moved
newly-purchased
granulator into
current location
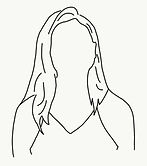
Fall 2018
Lauren Irie
was hired to
lead the team

Spring 2019
Successfully 3D
printed recycled
filament in Type
A for the first
time

Fall 2019
Collaborated with Engineers for a Sustainable World to form a team to work on the project

Fall 2019
Purchased new Monoprice Mini 3D printer
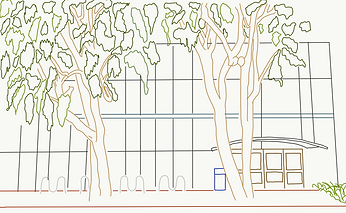
Spring 2020
Moved production temporarily into the O'Brien Hall labspace

Spring 2020
In-person research halts due to Covid-19, the team switches to remote projects
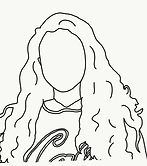
Fall 2020
Brooke Chang
was hired to
lead the team
This project began in 2016 when Nikki Panditi and Scott Silva of the Zero Waste Research Center (ZWRC) applied for The Green Initiative Fund (TGIF) funding for an extruder device to create 3D Printer Filament from failed 3D prints. At the time, however, the team was working with a smoothie blender as a granulation device, thus prompting the team to fundraise for an industrial grinder through a UC Berkeley crowdfunding campaign. When Nikki graduated from UC Berkeley in 2018, Lauren Irie took over Nikki’s place as the ZWRC 3D Printing Researcher and spearheaded the research and development of recycled PLA filament. Lauren applied and received a TGIF mini-grant in Fall 2018 to help fund these initiatives. By the Spring of 2018, she made her first batch of recycled PLA filament that successfully 3D printed. In Fall 2019, Lauren collaborated with Engineers for a Sustainable World (ESW) at UC Berkeley to form a team of engineers to assist her in increasing and improving the production of high-quality PLA filament. In the Fall of 2019, the team purchased a new Monoprice Mini 3D Printer in order to increase their printing speeds and prepare for mechanical testing of the printed recycled filament. In the Spring of 2020, production was temporarily moved to the O'Brien Hall lab space. In March of 2020, all in-person activities on campus were shut down due to the Covid-19 pandemic, and the team switched all efforts to remote research. In the Fall of 2020, Brooke Chang was hired as the ZWRC 3D Printing Researcher and took over to lead the team through the first fully remote semester in UC Berkeley history.
Our objectives for establishing this system are:
-
To establish a closed-loop recycling system for the University of California, Berkeley to efficiently reuse plastic-based products for educational resources on campus, in efforts of working toward the UC’s goal of Zero Waste by 2020;
-
To expand the interdisciplinary efforts of sustainability and technology, and create innovative ways to handle waste using modern engineering mechanics;
-
To, in an economically-sound manner, provide UC Berkeley with quality filament created out of recycled plastic material
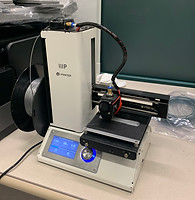


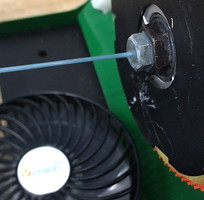
[1] The Recycling Association. “Chinese Customs Department Using X-Ray Machines to Check All Waste Containers.” The Recycling Association, The Recycling Association, Feb. 2017, www.therecyclingassociation.com/latest-news/national-sword-announcement.
[2] “Interview with Composting Manager of Republic Services.” 8 Oct. 2016.
[3] Lubow, Samantha. “Re: ‘Quantifying PLA Waste - How Much PLA Does Cal Dining Purchase?".” Re: "Quantifying PLA Waste - How Much PLA Does Cal Dining Purchase?", 3 Nov. 2017. Cal Dining Sustainability.
[4] Hesse, Brendan. “ABS or PLA: Which 3D Printing Filament Should You Use?” Digital Trends, Designtechnica Corporation, 25 Sept. 2015, www.digitaltrends.com/cool-tech/abs-vs-pla-3d-printing-materials-comparison/.
[5] Shen, Jennifer J. “Comparative Life Cycle Assessment of Polylactic Acid (PLA) and Polyethylene Terephthalate (PET).” Comparative Assessment of PLA and PET, 2011.